Products & Services
We provide a comprehensive range of services to support our customers, each conducted by engineering experts
News & Insights
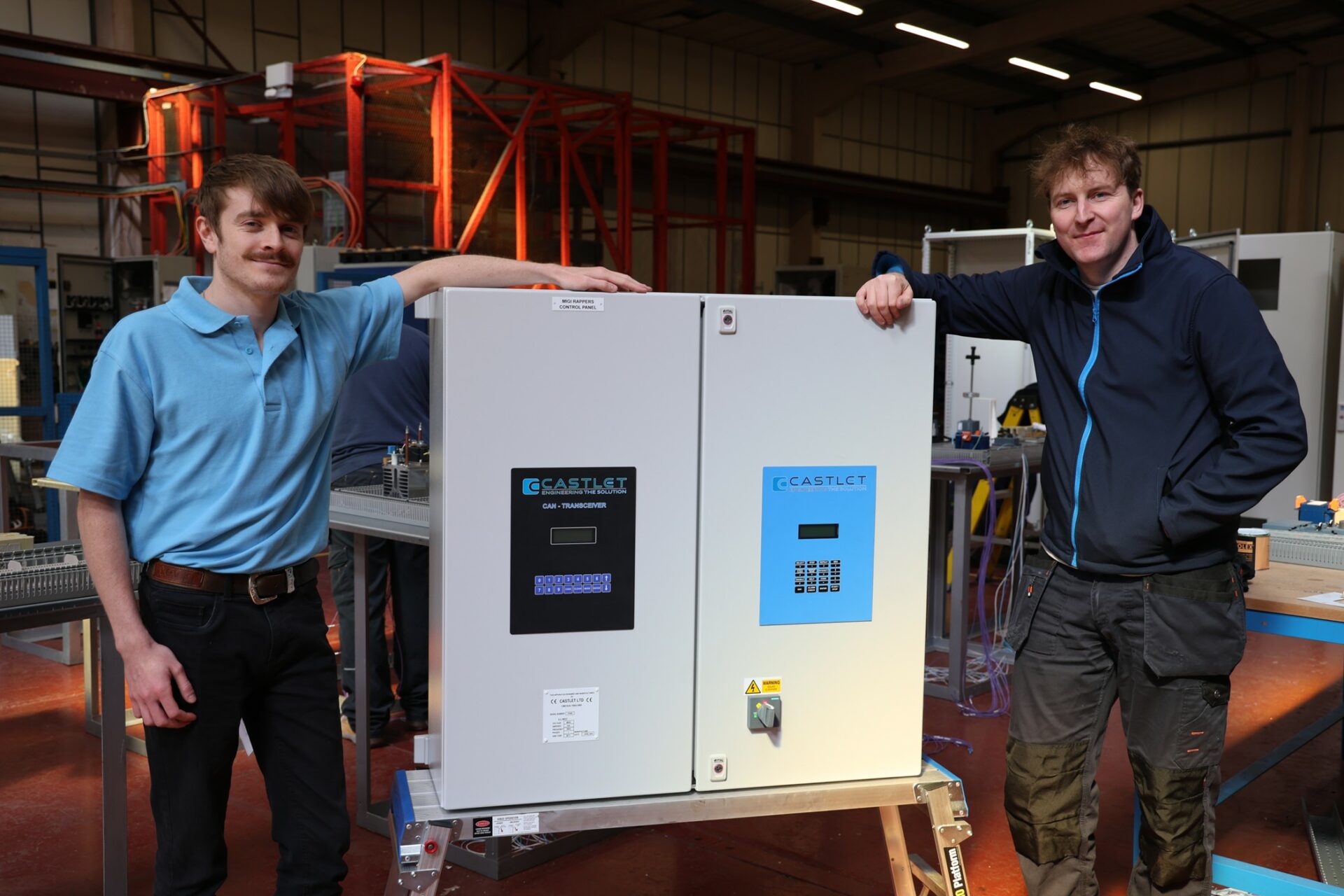
Reducing Maintenance Turnaround Time Using MIGI Rapper Control Panel for ESP Cleaning
Read more about how Castlet provided essential equipment for a world leading defence contractor.
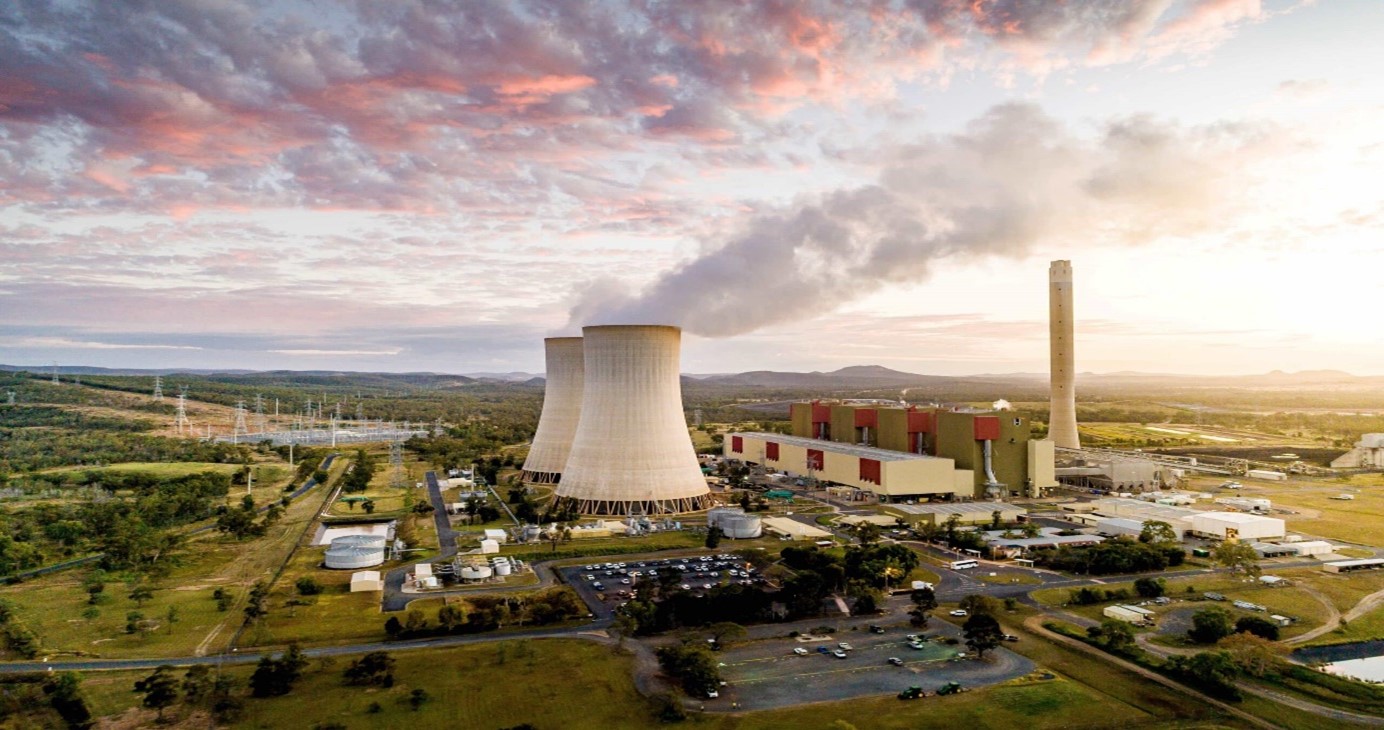
Extending the Lifecycle of Electrostatic Precipitator Control Systems at an Australian Power Plant
Retrofitting the electrostatic precipitator (ESP) control system at a power station in Australia.